WHAT IS LASER SCANNING?
Over the past few years, many companies in the AEC industry have widely adopted laser scanning technology. With the Covid-19 safety guidelines still in place, teams working remotely are heavily relying on laser scanning services for measuring and surveying sites now more than ever.
Laser scanning has gained popularity for capturing high-quality, existing conditions in a digital format that can be accessed from anywhere with the touch of a button. Laser scanners can effortlessly and rapidly capture any shape or object with complex geometric forms in a three-dimensional digital form with various laser points and lines. This scanned environment includes millions of data points presented together as point clouds with X, Y, and Z coordinates to enable a user to create the most accurate 3D models. We’ll talk more about point clouds in a moment.
Further, laser scanning can be implemented during various project stages from design to construction, renovation, demolition, and more. Many professional laser scanning service providers also offer scan-to-BIM services that streamline the process of data collection and drawing development. We at ENG offer high-quality, detailed, ready-to-use 2D drawings and 3D models. Get in touch with us today to find out how we can assist you with your next project.
Laser scanning technology involves various phases, from scanning and registration to deliverables management and more. In this article, we’ll do a deep dive to understand how laser scanning works and the types of data formats this technology offers. In part 2 of this article series, we’ll cover the other aspects of laser scanning technology, such as the work done pre-site and on-site, registration, required product licenses, and so on. Let’s get to it!
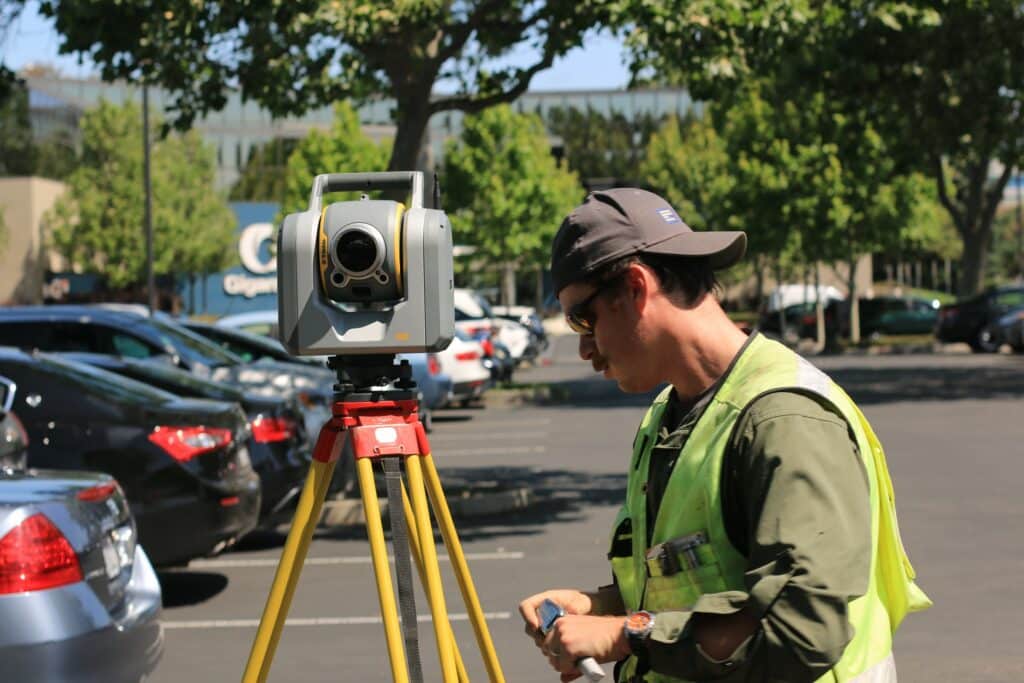
HOW DOES LASER SCANNING WORK?
Laser scanning technology has continually evolved over the past few years to offer faster and accurate scanning results with enhanced precision.
A 3D laser scanner is a terrestrial rotating device set atop a tripod. Once it’s activated, the scanner spins at high speed, emitting a low-energy, infrared laser light with high precision onto a rotating mirror that captures 360-degree images of the surrounding environment with light.
The laser head sweeps across the area, reflecting every object in its path back to the scanner, recording about one million data points per second with a typical spacing of 1 to 3 mm. The resulting data is a point cloud vector image containing detailed measurements in X, Y, and Z coordinates and RGB values for each point.
Laser scanners today use laser beams, advanced sensors, Global Positioning Systems (GPS), Inertial Measurement Units (IMU), receiver electronics, and photodetectors to calculate the most accurate coordinates of any surface, structure, or surroundings.
TYPES OF LASER SCANNING DELIVERABLES
The scanned data is presented in two ways: Point Clouds and 360 Pictures. Let’s take a closer look at each of these deliverables.
1. Point Clouds
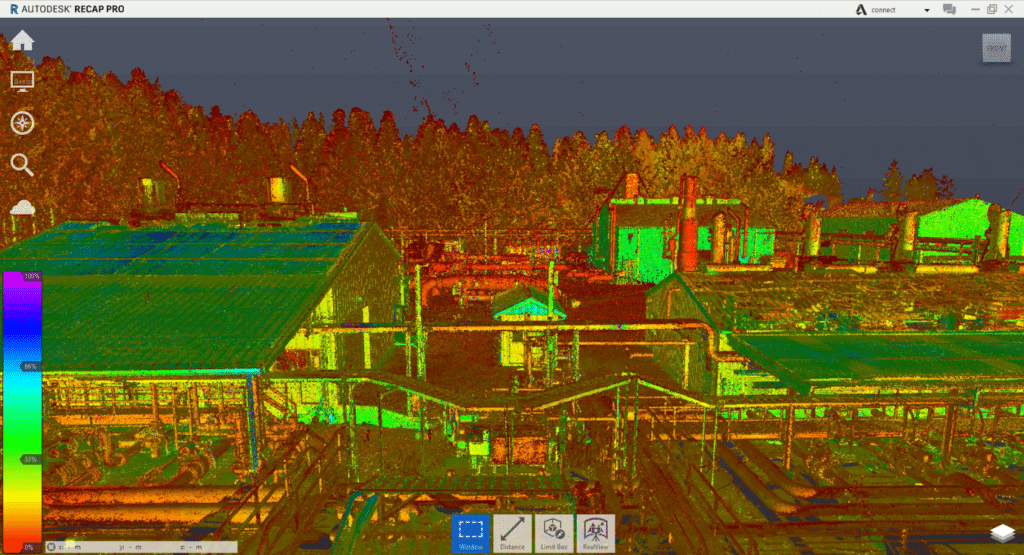
The laser mapping process captures a large volume of 3D survey points of any given object or surface. This gathered data is referred to as the Point Cloud. These data points are converted into standard file formats through a process known as registration or stitching. They can be viewed as 3D models on various software applications such as Recap, AutoCAD, Revit, Navisworks, Bentley MicroStation, etc. Also, these point clouds can be available in different file formats like .ptx, .e57, .rcp, .rcs, .xyz, .pts, .pod. Point clouds can be used to create both 2D drawings and 3D models.
With millions of data points captured, a point cloud file can be quite large to work with, which is a common concern expressed by many users. To reduce the file size, point clouds can be decimated, which works by removing points based on spacing and percentages. Typically, point cloud processing software comes with the ability to decimate files based on set parameters, but this should be done carefully as incorrect decimation can affect the quality and functionality of the finished product.
If you’re using Autodesk’s Recap, the default resolution for its files is 5 mm between points. However, it also allows you to choose a resolution between 1 to 100 mm. So, it’s up to the user to determine whether they need a file with a tight resolution for additional details or lighter file size for ease of use.
- Greyscale and Colored Point Cloud
This color scheme refers to the point clouds presented in applications like Revit, TruView, or Jetstream. The scanning is black-and-white and you can set it to take a photo to get a colored point cloud. But, for construction- based laser scanning, you need to agree with the client on what they need first. When an object is scanned, it’s assigned a greyscale value from 0 to 100 based on its reflectivity and the angle of incidence.
What’s interesting is that laser scanning doesn’t require the spaces to be illuminated. It can perform reality capture in a pitch-dark environment.
In addition, a laser scanner can capture spaces in full color as well. After the initial capture is complete, the built-in digital cameras in the scanner perform a second sweep of the area to capture hundreds of tiny pictures stitched together to form a color, stereoscopic picture.
The processing software then colorizes the scanned 3D data points to deliver a full-color 3D point cloud. However, a laser scanner requires spaces to be well illuminated to capture the stereoscopic pictures.
The important thing to keep in mind is that color scanning takes thrice as long to complete compared to greyscale scanning and the file sizes are significantly larger to view and process and therefore, the color scanning prices tend to be higher than the default greyscale documents. Please feel free to reach out to us for inquiries about our color scanning services.
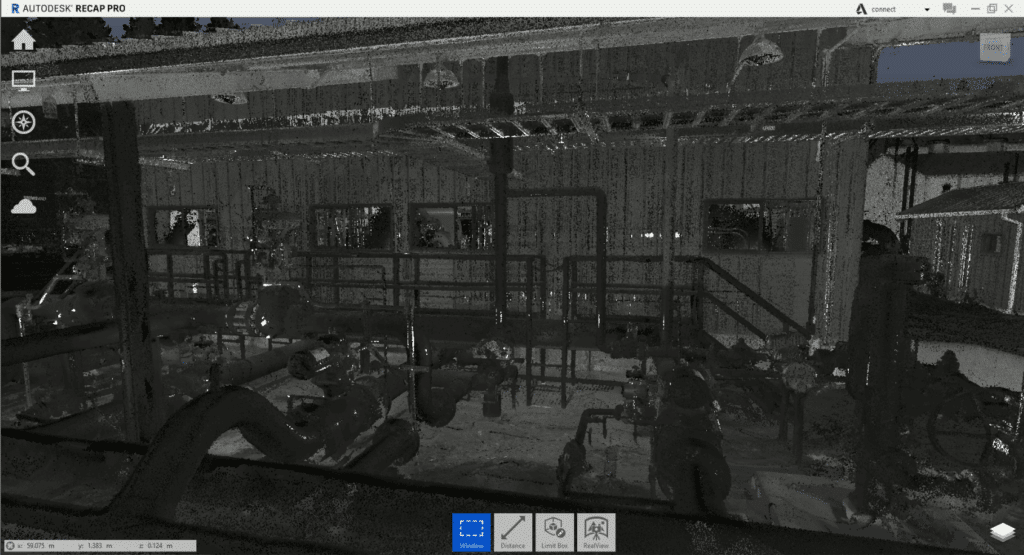
- Structured or non-unified Point Cloud
Structured or non-unified scans originate from terrestrial or tripod laser scans. The scanner records individual locations of scan positions, real views, and depth maps with corresponding X, Y, and Z coordinates of each pixel in the panoramic image grid. A structured scan enables creating mesh models from captured data, where each point can be visible in the 3D space.
Structured scan data is typically produced by devices like Faro, Leica, Z+F, Riegl, Topcon, and Trimble and supports file formats like .FLS, .PTG, PTX, ZFS, CLR, RSP, and RDBX.
- Unstructured or unified Point Cloud
Unstructured or unified point clouds are typically generated using mobile lidars and drone-based photogrammetry. The data originated from these devices is unstructured because there are no scan positions associated with a depth map, unlike tripod scans. Unified data combines all the scans into one individual scan file.
Unified scans lose the “structure” of the project and panoramic images. Scan positions are no longer visible in the 3D space. This affects the quality of the scan and makes the overall file size slightly smaller and somewhat easier to operate on modeling applications like Revit.
Every point cloud software has the option to generate a unified point cloud. Structured data can be converted to an unstructured point cloud, but the reverse isn’t possible.
2. 360 Pictures
Like point clouds, 360 Pictures is another deliverable offered by laser scanning technology. 360 pictures have an added advantage as it allows users to perform a walkthrough multiple times as required right from the comfort of your desk. Depending on the software deployed, it offers several other options like markups, attaching additional information like images, PDF files, etc. With 360 pictures, all the surveyed information can be accessed remotely for collaborative work.
360 color pictures are usually specified in conjunction with point clouds for additional survey recording. These images can be combined with the 3D scanned data points to appear scalable.
These color images can be installed on your local computer to create portable 360-degree panoramic views of your scanned data. This is especially beneficial when you’re on the go and are unable to load the scanned data to a cloud-based resource or dedicated server. To access these images, you can simply use your web browser to install Adobe flash plug-in and instantly view the scanned data.
Using software applications like TruView, images can be enlarged and rotated to view specific details and site dimensions. It can also be used to detect structural defects like cracks, sagging beams, a bulge in walls, which could otherwise be missed on site.
Other Ultimate Deliverables
Other types of deliverables can be created from the point cloud and this will depend on the initial scanning purpose. Weather it is a base model for 3D model coordination or a record model for an existing facility, the process of creating these deliverables is quite the same. Let’s see how this works:
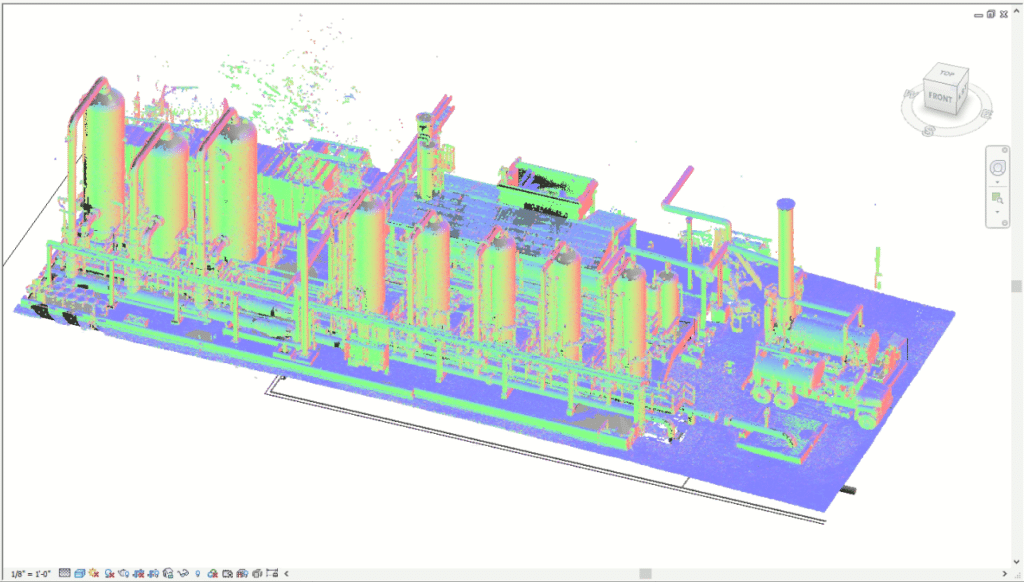
- From Laser Scan to 3D Models
The scanned data of existing building fabric can be utilized to create sophisticated 3D BIM models. Broadly speaking, the resulting point cloud is linked in Revit where, by using different views and modeling techniques, the modeler starts tracing the points to build the 3D digital geometry of the required building components. Creating 3D models from point clouds requires high precision and experience; professional survey firms with a good track record like ours can deliver these documents effortlessly.
Using scanned survey data for developing complex 3D models of existing and historic buildings has never been easier as scanned data can be directly integrated from point cloud to drafting platforms like Revit.
- From Laser Scan to 2D Models
After creating a 3D model from the point cloud using an application like Revit, you can extract 2D representations of the geometric forms and annotate them to produce a complete set of as-built 2D drawings. Further, you can add more details to the 2D drawings, such as floor tags, material specs, pipe elevations, and so on, to create finished documents. As these drawings are generated from 3D models, the process of developing base drawings is achieved in a matter of minutes!
FINAL THOUGTHS
Over the years, laser scanning services have become more affordable and commonplace throughout all design and construction phases. There’s no denying that it’s a versatile tool capable of saving thousands of dollars by minimizing errors, rework, and change orders. Moreover, incorporating point clouds into your workflow offers remote workability for all stakeholders and helps keep the projects on schedule.
As a part of the evolving AEC industry, it’s in your best interest to keep an open perspective about the technological breakthroughs in the market and leverage them to stay ahead of your competition.
If you’re thinking about implementing this cutting-edge technology for your next project, think ENG! Please get in touch with us today to determine how we can deliver on your scanning and documentation goals!
Do you want to continue reading about this topic? Don’t miss part 2 of Everything You Need To Know About Laser Scanning For The AEC Industry (Part 2)
ENG
For more information, contact us!
E-mail: eng@engbim.com
Call us: (949) 340-6924