What if tomorrow’s construction solutions could be implemented today? ENG’s latest case study shows how VDC and robotics make this vision a reality. In the recent case study webinar “Tomorrow Happening Today,” ENG partnered with experts from Alston Construction company and Dusty Robotics. Together, they showcase how combining advanced technologies with Virtual Design and Construction (VDC) leads to remarkable outcomes. Thus, this case study demonstrates how these innovations deliver cost savings and significant schedule reductions. The discussion centers on overcoming demanding customer requirements, implementing strategic technologies, and achieving measurable results with best practices.
The webinar featured Ricky Molina, VDC Director at Alston Construction, Zachary Reis Davies, representing Dusty Robotics, and Maria José Diaz, BIM Coordinator at ENG, highlighting how ENG’s 500+ BIM specialists drive solutions throughout the building lifecycle. Get ready to explore the future of construction.
Project’s Overview
A U.S. warehouse client developed an automation system incorporating AI-driven technology and self-driving robots to optimize product storage and retrieval in distribution centers. Key features include a modular design that adjusts to new or existing distribution centers, autonomous operation with mobile robots and lift cells guided by AI, high-density storage that maximizes space utilization, and custom palletization for each store’s specific needs. Furthermore, as part of a phase-two system revamp within an existing, fully operational building, the project’s goals included:
- Increasing control onsite.
- Maximizing space in a confined, active area.
- Lowering production costs.
- Reducing workforce while maintaining precision and quality.
However, these objectives were not without challenges:
Traditional methods and underutilized tools failed to meet the project’s complexity, leading to discrepancies in precision between design and fieldwork. Furthermore, information was initially lost between the design and construction teams. Finally, the reliance on manual QA/QC checks extended the project schedule. As such, adopting advanced BIM solutions and Dusty Robotics’ 3D scanning technology became crucial in overcoming these barriers.
BIM Solutions and Automation in Construction: Key Innovations
To tackle these challenges effectively, the project team implemented cutting-edge technologies and solutions to ensure success.
· Enhanced Communication with CDE
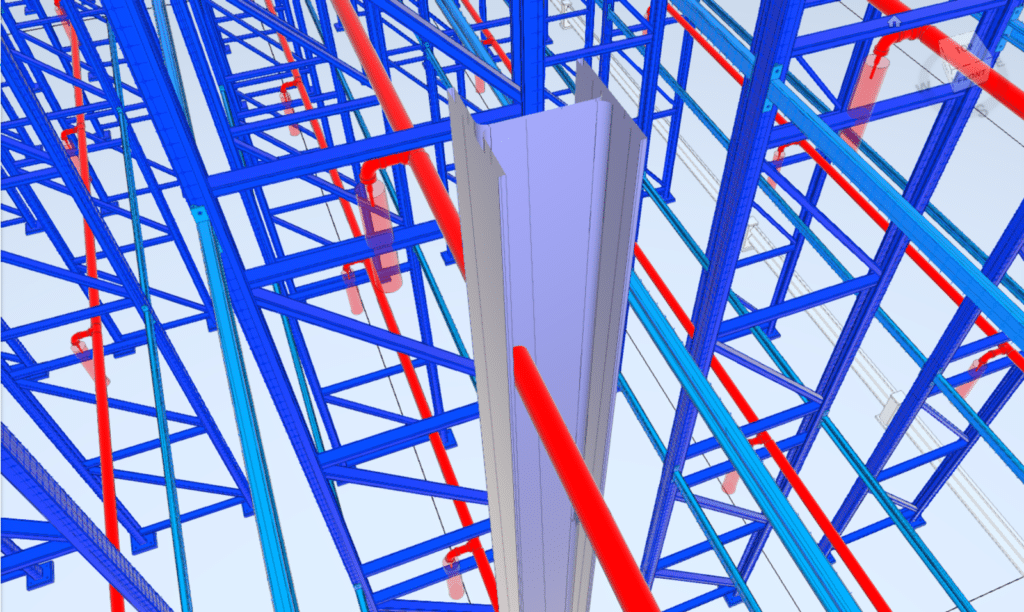
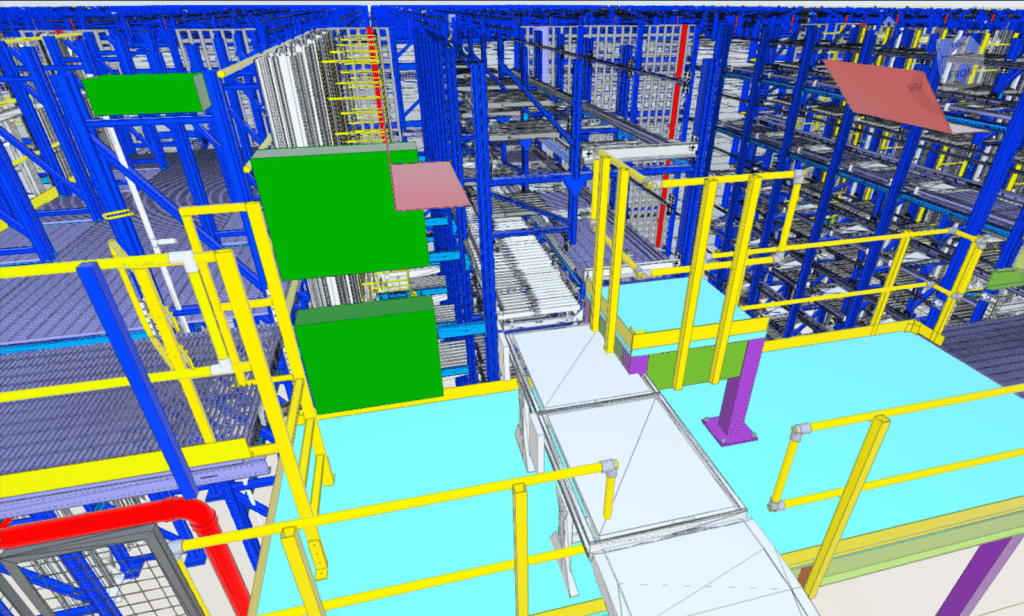
Maria José Diaz, BIM Coordinator at ENG, highlighted how establishing a Common Data Environment (CDE) was the first step in addressing underutilized tools. “We set the foundation by creating a centralized space in Autodesk Construction Cloud, where everything was organized according to our BIM Execution Plan,” Diaz explained. This approach ensured that all essential data from the design phase was captured and retained, particularly the LOD 400 Revit models, which were rich in information and instrumental in streamlining workflows.
The CDE allowed for more efficient supply chain management. “We broke down the Bill of Materials (BOM) by construction phase, enabling the supply and material team to move items from the laydown yard to the site as needed,” Diaz shared. This phase-specific material allocation significantly reduced construction time and resource waste.
Additionally, leveraging Revit models facilitated effective clash detection, particularly for electrical and fire systems previously limited to 2D drawings. “Once we consolidated all elements into a 3D Revit model, we could run clash detection, uncovering major issues like conveyors intersecting steel structures and fire pipes colliding with warehouse columns,” Diaz noted, underscoring the time saved in preempting these conflicts.
ENG utilized Autodesk’s Build module to standardize QA forms to enhance quality assurance, moving away from the previous Word-based, manual process. “The new forms enabled the QA team to conduct checks onsite using iPads, reducing time spent in trailers and increasing field inspections,” Diaz added. Automating Non-Conformance Reports (NCRs) and log generation improved accuracy, ensured comprehensive record-keeping, and boosted overall project efficiency.
· Automated Layout Precision with Dusty Robotics in VDC Projects
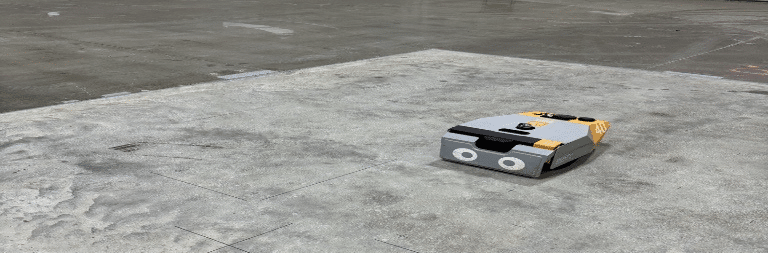
On the other hand, Ricky Molina, VDC Director at Alston Construction, emphasized the significant impact of Dusty Robotics’ Field Printer on improving layout precision. Furthermore, integrating this technology enabled the team to achieve layout accuracy within 1/16 of an inch, which allows autonomous robots to perform seamlessly and significantly reducing rework and installation time. The automated Field Printer allowed a single operator to complete the layout in just five days, one-third of the time traditional methods typically require, and with ¼ of the manpower necessary. As a result, this approach enhanced layout detail, minimized workforce needs, and boosted overall project efficiency.
· HoloBuilder for Real-Time Construction Tracking and Enhanced Safety
ENG also introduced HoloBuilder as an essential solution for capturing weekly construction progress with incredible speed, precision, and detail. “We needed a tool that could record the entire project’s progress in real-time,” María explained. HoloBuilder’s use of high-resolution 360° images enabled the team to document site conditions comprehensively, allowing stakeholders, regardless of whether they were onsite or not, to view the project’s past, present, and future states remotely. This innovative approach reduced reporting time from 10 hours to just 2, with only one person needed, compared to the four previously required. “It was faster, easier, and provided far more information,” added Diaz, highlighting how HoloBuilder not only streamlined progress tracking but also empowered the client with instant site visibility.
Project’s Outcomes
These solutions led to impressive outcomes, significantly improving efficiency, precision, and cost-effectiveness. Tools like Dusty Robotics’ Field Printer reduced workforce needs by up to 50%, while HoloBuilder’s automated progress tracking allowed for faster reporting with fewer resources, directly lowering project expenses.
Additionally, schedule reductions were realized through automated layout processes and centralized data management, which accelerated key phases of the project. This automation significantly compressed the schedule, cutting layout times by two-thirds and reducing reporting efforts from 10 to 2 hours per week. Moreover, enhanced precision improved project safety and minimized human involvement in high tasks.
Conclusion
At ENG, we believe that adopting these technologies is more than just an upgrade—it’s a strategic step forward for the entire construction industry. We deliver precise, efficient, cost-effective outcomes by integrating advanced BIM solutions and automation. We invite you to dive deeper into this case study by watching the full webinar video, where our experts share in-depth insights and real-world results. Discover how ENG’s tailored solution can transform your next project—streamline workflows, boost accuracy, and achieve better cost management.