What happens when you’re asked to prefab a semiconductor fab, the most complex manufacturing facility in the world… before there’s a field team—or even a prefab shop?
That’s the challenge ENG faced when partnering on a 2.4 million square foot semiconductor fabrication facility in Arizona — a hyperscale project defined by tight timelines, constant change, and 10 billion worth in construction.
And somehow, we did it — not once, but twice.
This is the story Ant Mulherin (Head of Electrical VDC at ENG), Andres Leon (BIM Engineer), and Jim Todd (Field Superintendent) shared at Advancing Prefabrication 2025 in Phoenix. Together, they walked through one of the most demanding MEP prefabrication efforts the semiconductor industry has seen. Furthermore, they unraveled the project’s success by focusing on three main pillars: early preconstruction planning, a resilient design-for-change mindset, and tight field-to-model communication workflows that bridged 1,296 miles of distance.
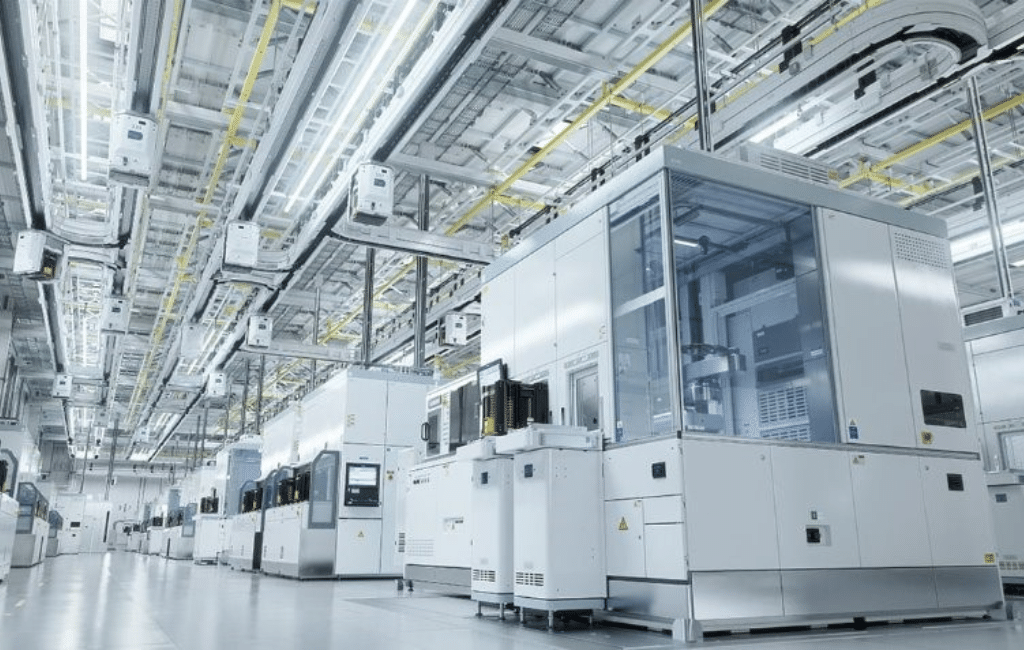
Why Is Semiconductor Prefabrication So Complex?
Before diving into the details, let’s talk about context. When ENG joined the project back in 2021, encompassing two massive semiconductor fabs housed in a single structure, the team was brought in early to shape the roadmap — with a clear focus:
Design and plan the telecom prefabrication effort from the ground up, electrical came later on.
It’s worth mentioning that if you haven’t worked in semiconductor fab construction, the term “fab” might be unfamiliar. Short for fabrication plant, it’s where microchips—the brains of our modern digital world—are manufactured.
But don’t let the word “plant” fool you. These are not typical industrial buildings.
“These are, I kid you not, the most complex manufacturing facilities in the world… it’s really hard to overstate the scale of these things.” – said Ant Mulherin, Head of Electrical VDC at ENG
He wasn’t exaggerating.
Fabs are multi-billion-dollar, multi-year construction undertakings with:
- Five unique levels, each essentially its standalone project
- 600,000 square feet per level
- Dozens of interdependent systems, trades, and workflows
- Microscopic tolerances to support nanometer-scale technology
And the kicker? ENG had to start six months before anyone set foot on site.
Preconstruction Planning and Design-for-Change in Prefab
When it comes to the specifics, let’s start by saying that high-tech clients always expect more than technical execution. They want partners who can adapt quickly, collaborate digitally, and confidently navigate evolving project scopes.
Luckily, even in 2021, ENG already came equipped with an advanced BIM and VDC toolset: Recap+, Dynamo, and a full suite of cloud-based BIM workflows. These platforms enabled real-time VDC coordination across geographies and time zones.
Of course, digital tools alone don’t deliver prefab — execution strategies do. That’s where field leadership stepped in. Drawing from decades of experience, Field Superintendent Jim Todd introduced a proven “top-down construction” approach to guide early design.
The result was a comprehensive “detail book” — over a thousand pages of sheets — that provided clear install instructions for both prefab and stick-built scenarios, giving the field maximum flexibility. If prefab wasn’t feasible in a certain zone, the same deliverable could still support a manual install — no redesign, no delays, no extra requests. It was a deliberate safeguard against the unpredictability of hyper-scale projects and a defining example of ENG’s design-for-change philosophy in action.
Field Communication — The Real Engine Behind Remote Prefab
Even the most polished prefab kits and coordinated models will fall short without one critical element: field communication. ENG knew the traditional “stick build” mindset wouldn’t work on a project of this scale. Moreover, Electricians couldn’t just glance at a drawing and make it up as they went — not with thousands of devices, tight tolerances, and prefab kits arriving in coordinated waves.
Therefore, ENG implemented structured daily video calls where field crews could walk through specific areas in the model, ask detailed questions, and mark up live PDFs. These sessions weren’t one-way updates — they were interactive checkpoints where field installers, modelers, and superintendents worked as a single unit to validate constructability in real-time. Since crews weren’t using Navis or Revit on site, all information had to be delivered clearly on 11×17 PDFs — every measurement, every material callout, every prefab detail.
Through these sessions, ENG ensured that the field always knew what was coming and had the opportunity to flag issues or conflicts before they became costly delays. That visibility — both digital and human — was the engine behind field buy-in and, ultimately, the success of the prefab strategy.
The Second Fab — Applying Lessons Learned, in Real Time
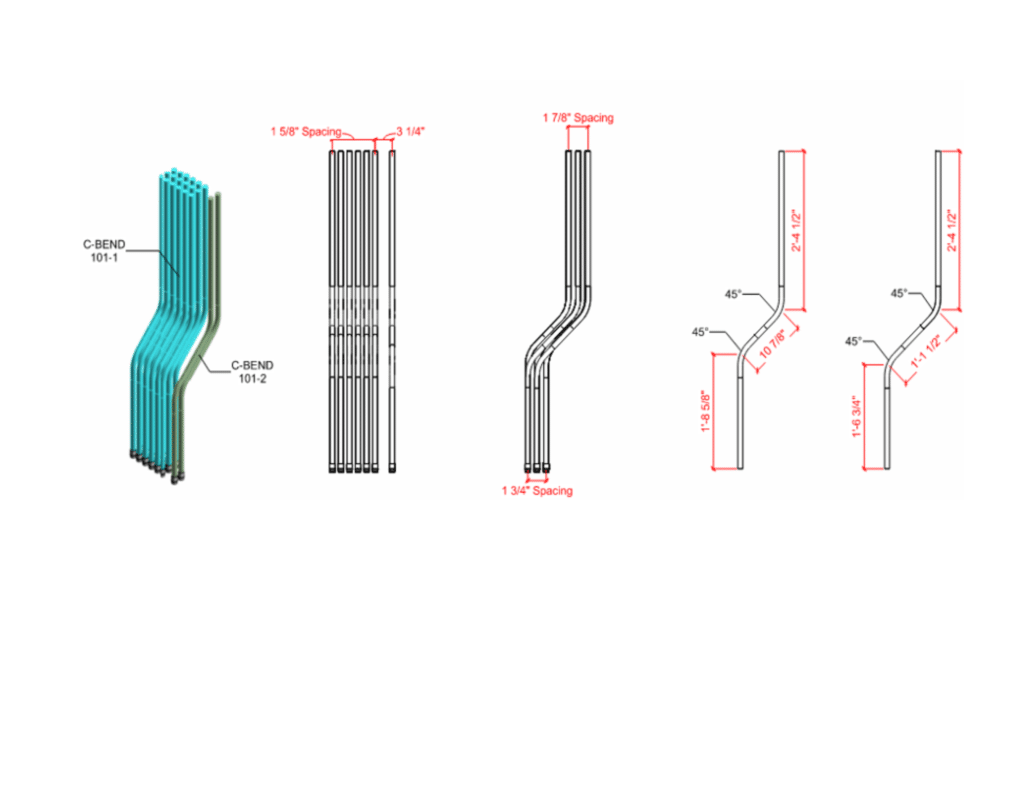
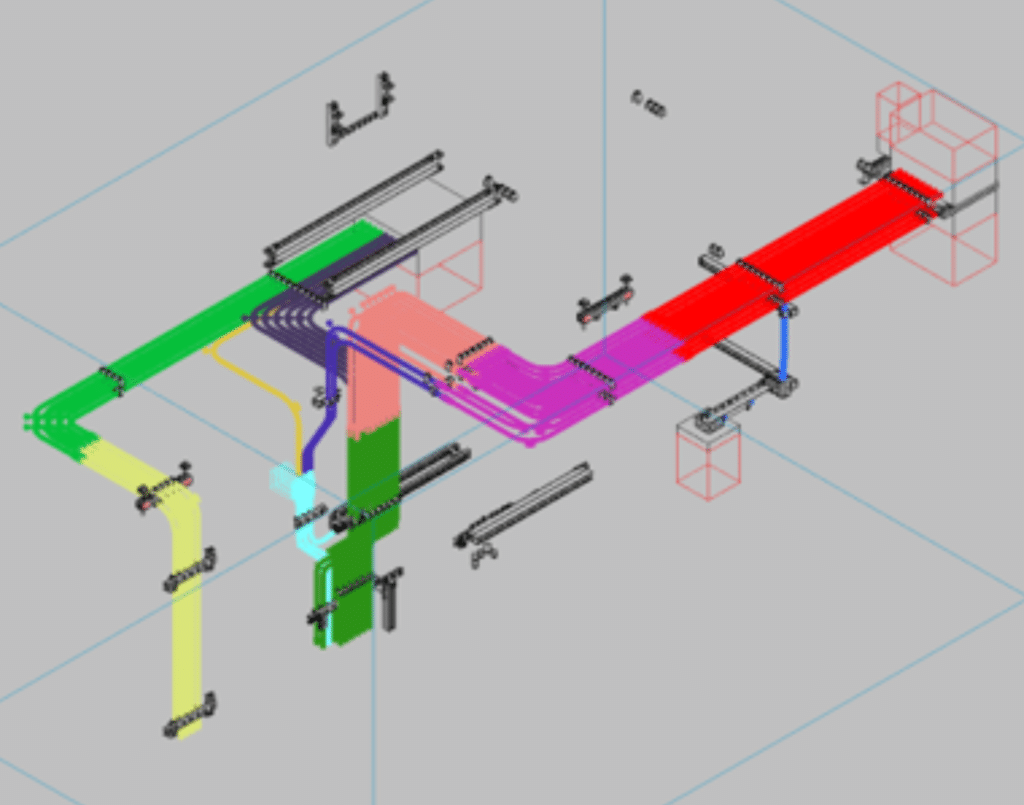
While the first fab was still under construction (around 70% complete), the second fab began. As a result, ENG performed what the team jokingly called “time travel”. Taking lessons from an incomplete experience and applying them to a brand-new, equally complex building. “We spent a year reworking and making mistakes,” said Andres León, BIM Engineer at ENG. “But by the time we started the second fab, we had the families, the workflows, and the field feedback to standardize confidently.”
The results speak for themselves:
- From 993 to 132 prefab kit types — 10x simplification
- 1,500+ devices installed per fab using repeatable kits
- One prefab type reused 300+ times on a single-level
- 250+ hours saved using AI+Dynamo-powered automation
- Zero slowdowns during scale-up from 7 to 40 team members
- Additional electrical scope awarded by the client mid-project
More than just metrics, these outcomes reflect ENG’s core belief: invest early, adapt quickly, and scale what works — because prefab only delivers value when it’s built for the real world.
Key Takeaway: Building a Prefab Semiconductor Fab That Works in the Real World
This project wasn’t just a technical milestone—it was a case study of how early planning, digital innovation, and relentless field alignment can transform how to approach prefabrication at scale. From day one, the success of the two semiconductor fabs depended not just on delivering accurate models but also on building a system that could flex, adapt, and work for the people actually installing it.
The guiding principle throughout was simple: build BIM for the field. Because if it doesn’t work on-site, it simply doesn’t work — no matter how good it looks in the model. By investing in standardization, automating the repeatable, and keeping field teams front and center, ENG delivered not just prefab — but prefab that was used at scale and with high impact.
Want to see how ENG pulled off one of the boldest prefab feats in construction history — without a shop or field crew?
Watch the full story below.
Webinar: How to Prefab a Fab… Have You Tried Time Traveling? | MEP Prefabrication Strategies