Tackling a project without detailed plans is no small feat, but it was a thrilling challenge for ENG’s Laser Scanning and Scan-to-BIM team. Armed with only a Google Maps pin and the total square footage, the team successfully digitally captured a vast central utility plant serving a prestigious East Coast campus. This article chronicles ENG’s expertise and strategic journey, led by Mariana Jimenez, illustrating their commitment to precision and their role in advancing facility management solutions through cutting-edge BIM processes.
Turning Limited Data into a Digital Asset with Scan-to-BIM
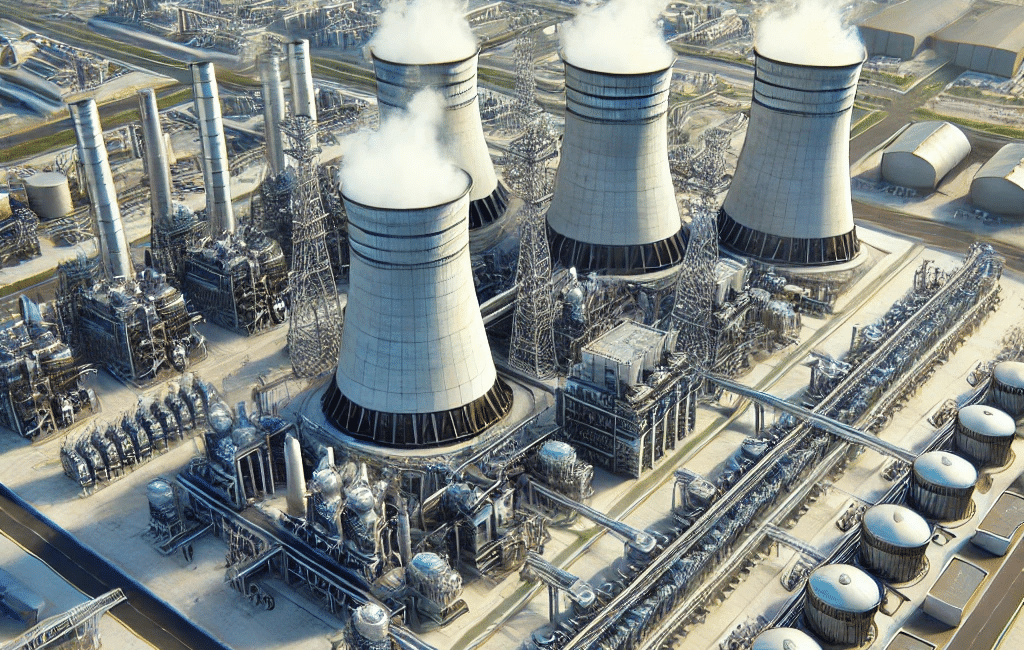
From the beginning, the team faced a pressing question: How do you accurately estimate a project of this scale with minimal information? Therefore, as Mariana Jimenez explained, creativity and risk management were key to navigating these uncertainties. “In projects where we start with so little data, identifying potential risks and developing strategies to mitigate them is essential,” Jimenez shared, drawing from her extensive experience.
The project’s primary goal was to create precise as-built 3D models to support future design, planning, and 4D scheduling for ongoing and future capital improvement projects. Moreover, these models were crucial for enhancing long-term facility management. The scope of the project was ambitious, requiring the team to scan the plant’s interior, façade, and rooftop across 7 levels despite limited specifications, such as an undefined Level of Development (LOD) and missing conduit dimension details.
Key Project Objectives: Accurate 3D As-Built Models
In addition to adaptability and innovative thinking, informed assumptions were essential when faced with a project scope that felt like a puzzle with too many missing pieces. Driven by the project’s objectives, the ENG’s team relied on informed assumptions to fill in the blanks and ensure every detail was covered. After numerous client discussions and several rounds of proposal revisions, critical decisions were made to shape the project’s success.
- Level of Development (LOD) 500:
The goal was to capture the plant’s physical attributes and compile comprehensive asset data. Hence, this approach created a true digital twin to support facility management.
- Essential Drawings for Effective Facility Management
Accurate drawings were essential for effective communication between the modeling team and the client’s onsite contacts, facilitating the seamless exchange of vital FM data. Furthermore, they served as the foundation for aligning the as-built model with the facility’s actual layout.
- Enhancing Facility Management with COBiE File Integration
The team committed to delivering a COBiE file as part of the final handover, ensuring all FM data was efficiently organized and integrated.
- High-Resolution Laser Scanning for Detailed Pipe Integration
A minimum diameter of 2 inches for pipes and conduits was set to control the modeling scope and maintain pricing. Nevertheless, the team scanned with high resolution to capture even smaller components, allowing for easy integration into the Revit model without rescanning.
- Aligning Levels with Precise Survey Control in Scan-to-BIM
Survey control was non-negotiable to guarantee accuracy and seamless level alignment. This step ensured that the model accurately reflected the plant layout.
Overcoming Complexity: The Site Visit Experience
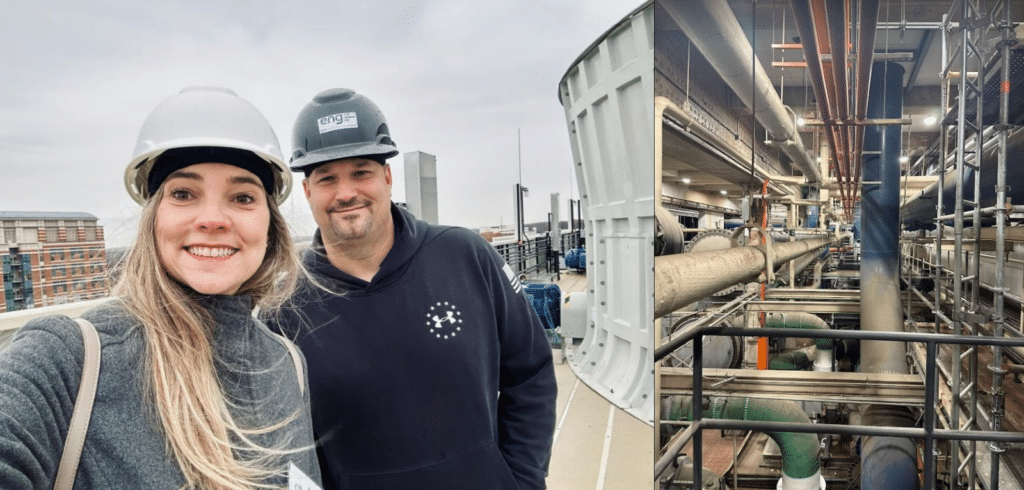
Since official drawings wouldn’t be available until after the bid was awarded, coordinating a site visit became a top priority. As Mariana Jimenez and the ENG team toured the facility, they were struck by its overwhelming complexity. Pipes and conduits crisscrossed every corner, and the machinery’s deafening noise echoed through the lower levels.
“The site visit allowed us to grasp the magnitude of the project fully,” Jimenez recalls. It became clear that the intricate layout required special attention to detail, particularly on the densely packed main operating level. The team captured images of exit plans near staircases to help guide their efforts.
Armed with these photos, videos, and floor plan snapshots, the team pieced together what they humorously referred to as their “Frankenstein set of floor plans.” While imperfect, this improvised set provided a basic sense of the building’s configuration, helping the team make high-level assessments of their scanning strategy.
Crafting the Final Proposal for Scan-to-BIM Success
Estimating this project was a challenging task, especially with limited upfront data. However, the insights gained from the site visit allowed the team to craft a tailored proposal that met the client’s exact needs:
Onsite Work:
- Duration: 20 days
- Team: 4 full-time technicians
- Tasks: Laser scanning and survey control
Data Processing:
- Duration: 25 working days
- Tasks: Data registration, clean-up, and file transfer
BIM Modeling:
- Total Hours: 3,200 hours over three months
- 15% of time allocated to project management and model quality control (QC)
As-Built Documentation:
- Deliverables: A comprehensive set of 50 as-built drawings
BIM for Facility Management (FM):
- Duration: 15 days
- Tasks: Data collection and labeling of systems and equipment in the models
COBiE File Creation:
- Duration: 15 days
- Tasks: Integration of FM data into a COBiE format
In summary, the article explores how ENG’s team tackled a complex Scan-to-BIM project with innovation, creativity, and precision. Follow the next part of the series to learn more about how this project was executed and the specific methodologies used!