In recent years, Building Information Modeling (BIM) has transformed the construction industry by enhancing precision, efficiency, and reliability in the design, installation, and maintenance of Mechanical, Electrical, and Plumbing (MEP) systems. By leveraging intelligent 3D models and data-driven processes, BIM enables professionals to streamline workflows, minimize costly errors, and enhance project delivery. Consequently, this article will explore how utilizing BIM for MEP systems improves accuracy and efficiency for optimizing installation and long-term performance.
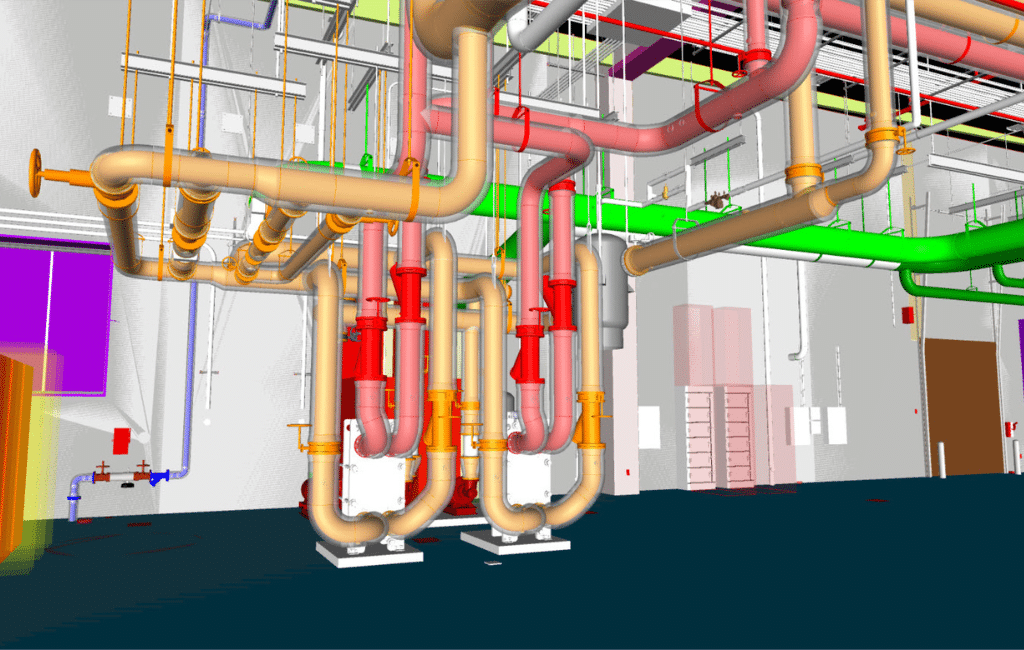
Comprehensive Visualization in BIM for MEP Systems
BIM unifies all MEP systems into a single, federated model, providing a comprehensive digital representation. Thus, it creates a detailed 3D representation of key components including HVAC ducts and pipes, electrical conduits, plumbing pipes, fire protection systems, and gas distribution networks, among others. When accurately positioning these elements in their spatial context, engineers and contractors use BIM to simulate real-world conditions and detect potential conflicts before construction begins.
For instance, in a hospital project, BIM ensures the precise placement of oxygen and medical gas pipes. These measurements prevent interference with HVAC ducts or electrical conduits within the same ceiling space. Likewise, in commercial high-rises, BIM helps engineers coordinate vertical risers for plumbing stacks, fire suppression pipelines, and telecommunications cabling, optimizing efficiency while avoiding overcrowding in utility shafts.
Ultimately, BIM provides a clear visual representation of MEP systems. Furthermore, it enhances spatial coordination, reduces costly rework, and improves project efficiency and safety
Clash Detection and Coordination of MEP Systems Using BIM and CDE
One of the most powerful capabilities of Building Information Modeling (BIM) is automated clash detection, which proactively identifies conflicts between the MEP components and structural/architectural elements before construction begins. As a result, BIM minimizes costly on-site modifications, reduces project delays, and ensures seamless system integration.
Automated Clash Detection and Resolution
BIM-powered software like Autodesk Navisworks, ACC and Revizto, use advanced clash detection algorithms to analyze spatial interferences. For example, clashes can be identified such as:
· Ductwork interfering with structural beams
· Plumbing pipes intersecting with electrical conduits
· Fire sprinkler mains clashing with HVAC ducts
Coordinated 3D models visually highlight these clashes, enabling project teams to conduct model-based coordination meetings and resolve conflicts before construction. By addressing these issues virtually rather than on-site, teams reduce rework, enhance efficiency, and maintain project timelines.
The Role of the Common Data Environment (CDE) in Coordination
While clash detection prevents conflicts, true coordination is achieved when all project stakeholders—architects, structural engineers, MEP specialists, and contractors—work from a single source of truth. This is where a Common Data Environment (CDE) becomes critical.
A CDE centralizes all BIM data in one platform. This ensures every team member can access the latest, most accurate models, drawings, and specifications. Thus, it eliminates data silos, outdated information, and miscommunication, which are major causes of project inefficiencies.
When integrating BIM-powered clash detection with a CDE, MEP systems are not only clash-free but also fully optimized, resulting in improved constructability, cost savings, and long-term operational efficiency.
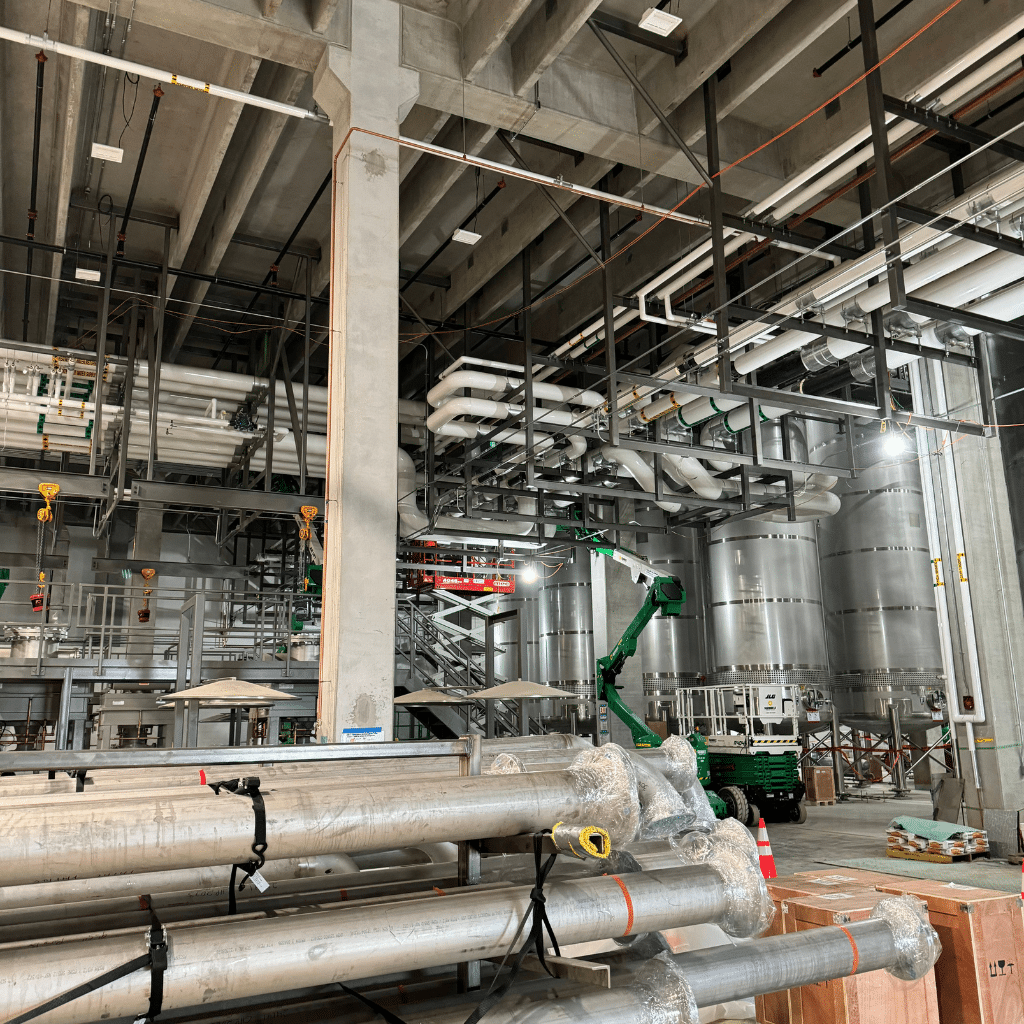
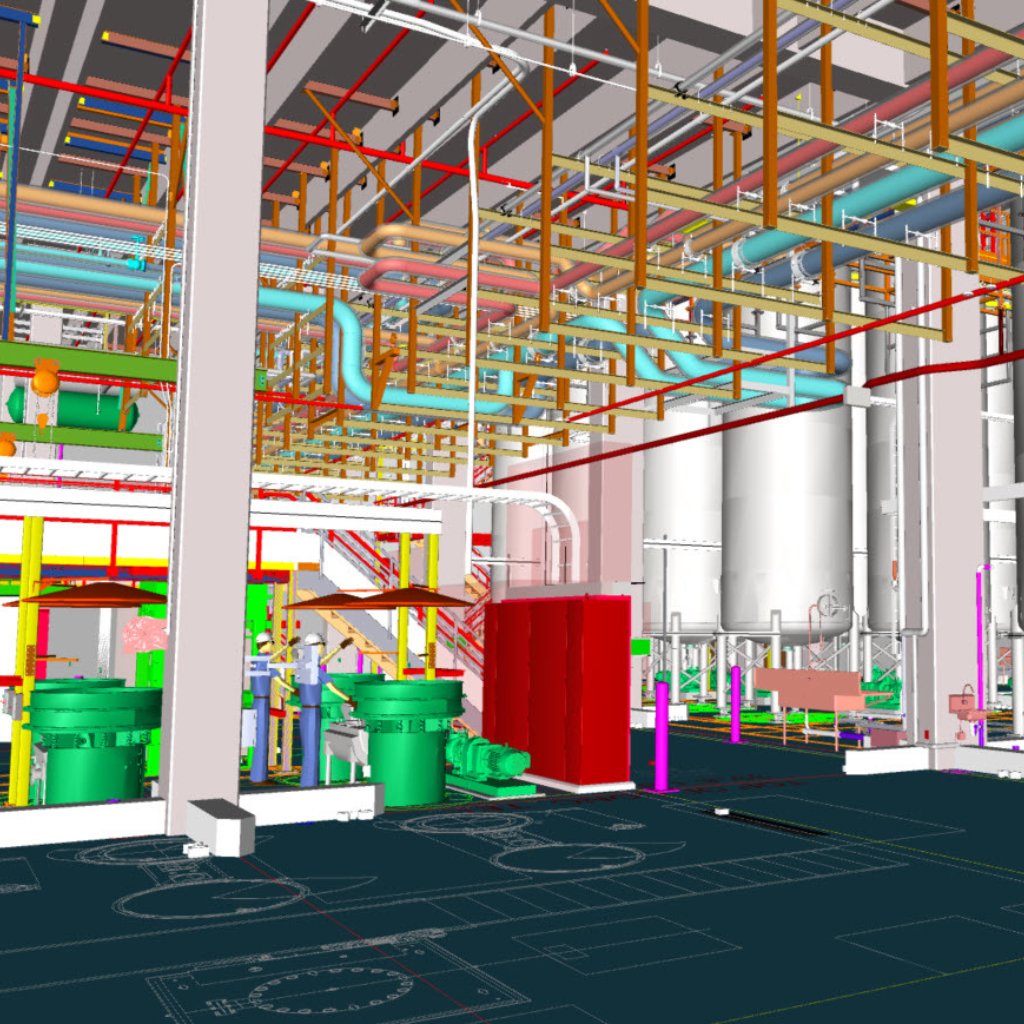
Virtual Design Construction for MEP System Optimization
Beyond clash detection, BIM enhances the accuracy, efficiency, and sustainability of MEP systems by leveraging data-driven analysis. With intelligent 3D models and real-time simulations, BIM provides precise material estimations, energy efficiency insights, and optimized space utilization for mechanical, electrical, and plumbing systems.
Mechanical System Optimization
· HVAC system components (air handling units, ducts, diffusers) are precisely modeled to ensure efficient air distribution without interference from structural elements.
· Chilled water and steam pipe networks are coordinated with electrical and plumbing routes to maximize space utilization.
Electrical System Optimization
· Electrical panels, bus ducts, and lighting fixtures are strategically placed within the BIM model to ensure proper clearance and spatial efficiency.
· Clash detection between electrical conduits and water supply lines prevents potential safety hazards.
Plumbing System Optimization
· Cold and hot water supply lines, vent stacks, and stormwater systems are designed within BIM. Ensuring efficient routing and compliance with building codes.
· Gravity-based drainage designs minimize material waste through careful optimization
By leveraging data-driven BIM analysis, MEP engineers can optimize system layouts, reduce material waste, and enhance overall building performance. Facilitate real-time communication among engineers, contractors, and other stakeholders.
Prefabrication for Faster and More Efficient Installation
BIM also plays a crucial role in prefabrication, reducing material waste and labor costs while improving installation efficiency. Additionally, allows for the preassembly of MEP components in a controlled environment, reducing on-site labor and installation time. Just-in-time delivery of prefabricated elements also reduces storage space requirements and site congestion.
As-Built BIM Documentation for Long-Term Asset Management
The primary goal of As-Built BIM is long-term asset management. Unlike design-phase BIM models representing intended designs, as-built models incorporate any changes, modifications, or deviations during construction. Therefore, it ensures that building owners, facility managers, and maintenance teams have an accurate digital record of the building’s infrastructure for future modifications, maintenance, renovations, and compliance.
Another benefit of As-Built BIM is planning for renovations and system upgrades. Systems degrade over a building’s lifecycle, new regulations emerge, and spatial reconfigurations become necessary. Without an up to date as-built record, facility teams often waste time and money conducting additional site surveys or dealing with unforeseen clashes during renovations. Yet, As-built BIM eliminates this inefficiency by providing a reliable, digital representation of existing conditions.
BIM for Facilities Management and Predictive Maintenance
In addition to traditional applications, BIM-driven Facilities Management (FM) and Predictive Maintenance are evolving into more data-centric, AI-enhanced systems. These advancements will optimize building operations in real time. Furthermore, integrating BIM with IoT (Internet of Things), Digital Twins, and AI-powered analytics transforms static 3D models into intelligent, self-updating platforms that support decision-making.
A key advancement is using sensor-enabled BIM models that track real-time data. From HVAC, electrical, and mechanical systems, machine learning algorithms use this information to predict potential failures before they happen. This condition-based predictive maintenance significantly reduces operational risks and extends the lifespan of building assets. Additionally, automated maintenance workflows—triggered through BIM-linked CMMS platforms—enable proactive scheduling, spare part forecasting, and labor optimization.
In large-scale facilities like hospitals and commercial buildings, spatial analytics within BIM help optimize energy use, occupancy management, and indoor air quality regulation. Furthermore, integrating augmented reality (AR) and mobile BIM applications allows on-site technicians to access live system data, visualize hidden MEP infrastructure, and execute maintenance with greater precision.
Looking forward, the evolution of BIM into a fully integrated Digital Twin ecosystem will further enhance real-time monitoring, self-learning maintenance models, and autonomous asset management. This evolution will set new standards for efficiency, sustainability, and cost optimization in the built environment.
Conclusion
In short, BIM enhances MEP system accuracy and efficiency by integrating 3D visualization, clash detection, and data-driven optimization. Moreover, it minimizes spatial conflicts, reduces rework, and ensures seamless integration with structural elements. Beyond installation, BIM-driven analysis improves energy efficiency, optimizes material use, and streamlines facility management through as-built documentation. When combined with AI, IoT, and digital twins, BIM enables predictive maintenance, reducing downtime and extending asset lifespan. By fostering collaboration through a Common Data Environment (CDE), BIM enhances project delivery, sustainability, and cost efficiency across the building lifecycle.
Are you ready to optimize your MEP projects with BIM? Explore ENG’s BIM Modeling Services or contact us for expert guidance!