As building projects grow more complex, many MEP contractors continue using manual coordination methods for planning, design, and execution. This choice persists despite the rise of advanced coordination technologies. However, outdated MEP processes struggle to handle the growing complexity of building systems and new technologies. These methods create inefficiencies in planning, increase errors, and delay projects. This article examines the key challenges contractors face when they use traditional MEP systems. It also explains why contractors must adopt MEP Coordination Systems to streamline project delivery and achieve better outcomes.
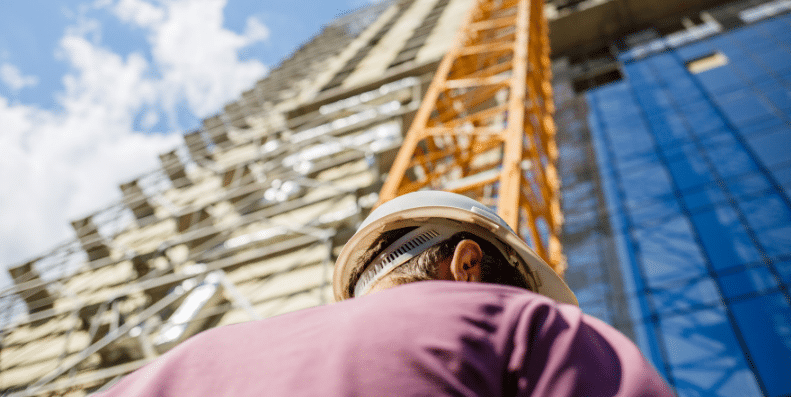
Understanding the Challenges of Traditional Systems in MEP Contracting
While traditional MEP systems have been successful, they have several limitations in today’s construction industry. Consequently, here are some of the most significant MEP coordination challenges faced by contractors using manual coordination methods:
- Addressing Inefficient Pre-Construction Design Reviews with MEP Coordination Teams: Traditional pre-construction coordination often involves many meetings with MEP teams, which are time-consuming and inefficient. These delays increase project costs. Using only 2D drawings creates incomplete or inaccurate system representations, making it hard to detect clashes before construction.
- Decentralized Design Responsibility: A Major MEP Coordination Challenge: In traditional coordination, fragmented design responsibility creates challenges. Different teams manage separate systems, which leads to inconsistencies and clashes during construction. A lack of a unified problem-solving approach increases delays and costs as teams resolve issues independently.
- Managing Expensive Rework Caused by Unexpected Changes in MEP Systems: Design changes during construction are common, but traditional coordination handles them poorly. Adapting to changes disrupts timelines and inflates costs, especially when major redesigns are needed.
- Tackling Sequential Tasks and Lack of Automation in MEP Clash Detection: Traditional coordination lacks automated clash detection, delaying issue identification and requiring costly rework. Sequential processes add inefficiencies by forcing tasks to follow a rigid order, further extending project timelines.
How MEP Coordination Systems Revolutionize Construction Planning
MEP coordination systems have transformed the construction industry by effectively addressing the MEP coordination challenges faced by contractors using traditional methods. These systems leverage 3D modeling and visualization tools to enhance clash detection and resolution, automate processes, and ensure alignment among stakeholders from the very start. As a result, the benefits of adopting modern MEP coordination systems include:
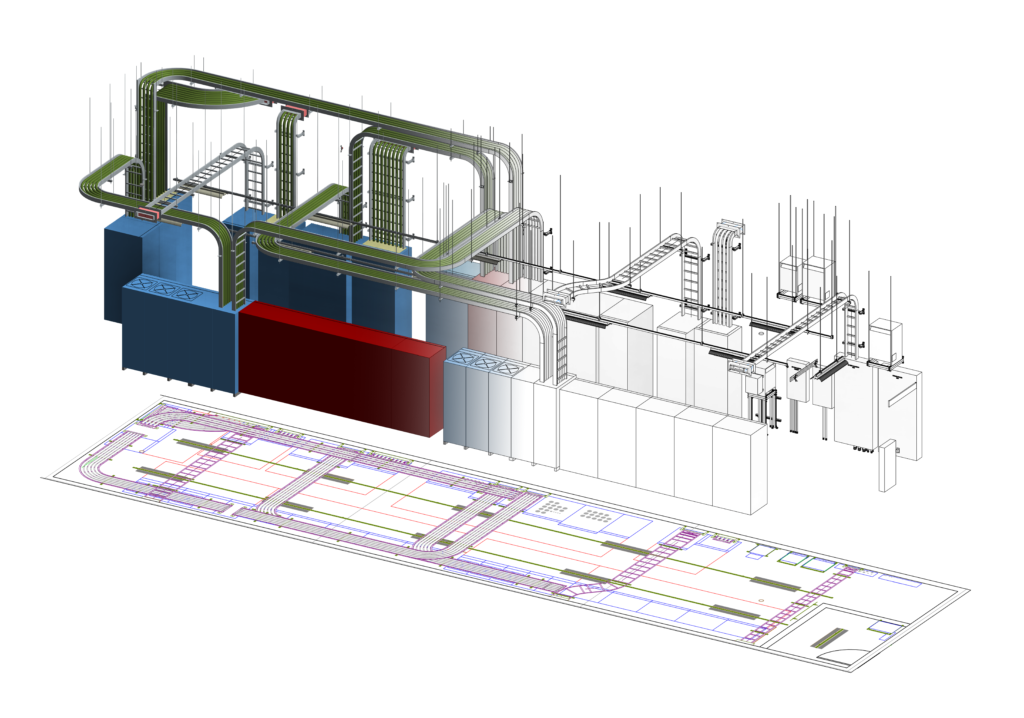
- Enhancing 3D Visualization of Clashes for Better Resolution: Modern MEP coordination systems use 3D visualization to help contractors quickly spot and fix clashes. Clear visuals of clash locations and severity allow adjustments before construction, cutting expensive rework and improving planning efficiency.
- Automating Clash Detection for Faster, More Accurate Results: Another key advantage is the automation of clash detection, which significantly reduces the time required for manual review. Moreover, the system accurately identifies potential clashes between different building systems and alerts contractors, ensuring that modifications are made before construction, thereby addressing many outdated MEP processes.
- Aligning Stakeholders During Initial Kick-Off Meetings: MEP coordination systems keep all stakeholders aligned during kick-off meetings. A centralized platform ensures clear communication, shared goals, timelines, and requirements, reducing miscommunication and construction delays.
- Ensuring Accurate Component Prefabrication for MEP Renovations: In addition, prefabrication becomes more precise with the use of MEP collaborative tools. These tools offer accurate measurements and specifications, enabling contractors to fabricate components off-site. Consequently, this approach minimizes the need for on-site modifications and speeds up the renovation process.
- Facilitating Precise Construction and Site Activity Planning: Digital coordination improves construction and site activity planning by providing detailed and accurate 3D models of building systems. As a result, contractors can plan the construction sequence, manage site logistics, and optimize resource utilization, ultimately improving overall project efficiency.
- Improving Facility Management with Up-to- Date System Information: MEP coordination systems provide accurate, real-time data on building systems to improve facility management. Facility managers use this information to maintain and operate systems efficiently, ensuring long-term success.
Ready to start your construction project with BIM MEP Coordination? Our experts can help streamline your project, reduce costs, and minimize errors.